FREQUENTLY ASKED QUESTIONS (FAQ)
What raw materials are required for production non-autoclaved aerated concrete?
Ordinary Portland Cement is suitable for production non-autoclaved aerated lightweight concrete blocks.
Fly ash: Fly ash is suitable for production. It is necessary to study technical parameters of available fly ash in order to define the fly ash type suitable for production.
Sand: Any available fine sand is suitable for production
What is the typical Mix Design?
1. Water
Following types of water can be used for production:
a) drinking water;
b) natural surface and ground water;
C) industrial water;
d) combined water, which is a mixture of water from two or more of the above sources.
The equipment should be able to heat the water to a temperature of 40-60C.
2. Cement
The following cement types can be used:
CEM I 32.5 R, CEM I 42.5 R or
CEM II/A-S 32.5 R
3. Sand (filler)
You can use river or quarry sand. It is recommended to use “fine” and “very fine” groups of sands (size of grains: 0.1 mm – 0.5 mm). Impurities (clay, silt) in the sand should not be more than 2%.
4. Aluminum powder or aluminum paste (Cell Generating Formula - CGF)
Types of aluminum powder: PAP-1 or PAP-2 (Russia); ARASAN-4, ARASAN-5 (India).
Aluminum paste: 5-7370/75V or 5-7370/75VS. The content of active aluminum should not be less than 75%. Dispersion of particles (D50 %) – 25-35 microns.
5. Caustic soda (controls the time of gas formation reaction)
Alternative names – sodium hydroxide (NaOH), sodium hydroxide.
The content of the active substance should not be less than 94%. With an increase in the amount of caustic soda, the reaction time of gas formation decreases and vice versa.
6. Sodium sulfate Na2SO4 (hardening accelerator)
Alternative name – sodium sulfate. The content of the active substance should not be less than 90%.
It is also allowed to use other hardening accelerators for concrete.
7. Forms greasing
The most inexpensive component of the grease – used engine oil.
The most affordable option for forms greasing is vegetable oil.
Special ready-made emulsifiers for concrete forms can be used as well.
What are main requirements for plant location?
When choosing a site for setting up production line, you should consider the dimensions of plant equipment and its power consumption.
The warehouse (shaded production area) should be bright and well ventilated. The required temperature in the production area should be around 20C.
Special attention should be paid to the absence of winds and disturbances (shakes, movements, etc.) in the place of aeration process of the formed mixture. The presence of disturbances can affect the entire production process, especially at the time of mixture aeration.
If the temperature in the production area is much less than 200C, it is necessary to achieve a temperature of 200C at least locally (in places of mixture aeration inside forms).
It is necessary to place the preheating chamber between the filling area and the cutting area. The optimum temperature in the preheat chamber should be around 35-40C.
The approximate size of the production area for easy operation of ECOCON-ASM-200CA plant is shown below (Fig. 1 and Fig. 2).
Fig. 1: General view of ECOCON-200CA plant

Fig. 2: Layout of ECOCON-200CA plant with production flow

Technological process of ECOCON-ASM-200CA plant (Fig. 2)
Phase 1. Unloading of ready-made products and forms preparation
№1-2. Labors take out ready blocks out of the chamber and place them on a pallet (2-4 minutes)
No. 3. Labor wraps palette with polyethylene film (1 min)
№3-4. Labors assemble form and lubricate it with oil (3 min)
No. 4. The labor delivers the assembled and oiled form for filling (1 min), takes away the pallet with blocks to the storage of ready-made products and brings up sand (if necessary).
Phase 2. Mixture preparation
No. 5. Operator-technologist controls the dosage of sand, water and cement, makes weighting of chemical components, prepares aluminum suspension (2-4 min)
No. 5. The operator-technologist drains the water, switches on mixer, loads all the raw components (2 min.)
Then the mixture is mixed in automatic mode (3-5 min.)
No. 5. Operator-technologist fills the form with prepared mixture and moves it into the chamber (1 min)
Immediately after unloading the components into the mixer, new portion of components automatically starts coming into dispensers for a new mixing cycle.
Phase 3. Forms removal and cutting
No. 6-7. Labors remove the sides of the form and drive the billet for cutting (2 min).
The cutting of billet into blocks is done in automatic mode (6 min).
No. 6-7. Labor cleans, lubricates sides of the form, and assembles the sides to the form Assembly post (3 min.)
At different stages of production, several actions are performed simultaneously.
What are main specifications of produced materials?
Non-autoclaved aerated concrete has several physical and chemical properties: average density, concrete compressive strength, thermal conductivity, drying shrinkage.
Average density.
Density of aerated concrete specifies what is the weight of 1 m3 of aerated concrete in a dry condition. Usually non-autoclaved aerated concrete is produced with following densities: 500 kg/m3, 600 kg/m3, 700 kg/m3, 800 kg/m3, 900 kg/m3.
Compressive strength.
This is a main indicator of compressive strength. In order to test the compressive strength of aerated concrete it is necessary to arrange from samples with sides of 100 mm, which are then kept for 28 days. Further test is carried out by compression of the received samples with the special press. The load that the sample withstand is the compressive strength of the aerated concrete. Strength of aerated concrete is measured in MPa (kg/mm2).
Table 1: Main technical specifications of ECOCON non-autoclaved aerated concrete.
Dry density, kg/m3 Compressive strength, MPa Thermal conductivity, W/m*C°
500 ________________________________________ 1.5 ______________________________________ 0.12
600 ________________________________________ 2.0 ______________________________________ 0.14
700 ________________________________________ 2.5 ______________________________________ 0.18
800 ________________________________________ 3.0 ______________________________________ 0.21
900 ________________________________________ 4.0 ______________________________________ 0.24
Advantages of using aerated concrete (taking into account hot and high-humidity climatic conditions).
1. Thermal conductivity.
The cellular structure of aerated concrete has a good heat-holding capacity. The lower the thermal conductivity, the better the material retains heat and coolness. In simple words, when it is hot outside, the house will have a comfortable temperature (it will not be hot). There is a substantial saving towards electricity cost when using AC units.
2. Large size of masonry units (600x300x200 mm) allows to do masonry quickly and easily, even without experience.
3. Light weight of masonry units - standard block with density 500 kg/m3 and dimensions 600x300x200 weighs 18 kg only.
4. Relatively high strength - strong walls of the house (aerated concrete blocks withstand heavy loads - 2-2.5 kg/mm2)
5. High vapor permeability - ensures clean air in the house. Aerated concrete is a breathable material, it removes gases and water vapor from inside the building.
6. Fire resistance - aerated concrete structure can withstand fire for more than 3 hours, while aerated concrete does not burn through. Very high rate for fire safety.
7. Environmental friendliness - aerated concrete is made only with natural non-organic materials and is safe for human health.
8. Good sound insulation up to 50 dB (with a wall thickness of 200 mm and density of aerated concrete 600 kg/m3).
9. Durability. The building of aerated concrete can last more than 100 years. The strength grows throughout the whole lifecycle.
10. Moisture resistance - not afraid of rain and storms, even if there is no lining. When you use veneer all the characteristics are maintained. In high-moisture conditions provides absence of fungus.
How does ECOCON plant work in general?
The materials in the concrete mixer (mixer-activator) are loaded in the following sequence:
1. Fill the mixer with water. The water temperature should be 45-60C.
2. Turn on the mixer.
3. Load cement into the running mixer.
4. Add caustic soda NaOH.
5. Add sodium sulfate Na2SO4.
6. Load the sand (filler)
7. Mix all above-mentioned components for 3-5 minutes
8. Add the prepared suspension of aluminum powder or a measured mass of aluminum paste (in dry form) and mix for 20 - 30 seconds.
9. While preparing the mixture, the form must be moved (rolled up) to the mixer. By the time of discharge of the mixture into the form it should be to cleaned, assembled and oiled. After the readiness of mixture, turn off the mixer and pour the mixture into the form.
10. After that, carefully, without sudden shocks, roll the form with mixture into the preheat chamber and wait for the moment of cutting the hump and removal of form’s walls (initial curing period). Initial curing period end should be checked with a penetrometer (device to test strength of the material).
11. After the shutter closing the cycle is repeated.
12. After getting the required strength, the form is rolled out of the preheating chamber, the form’s walls are removed and billet is cut into separate blocks.
13. The cut-into-blocks billet is moved to the secondary curing chamber to gain strength. Exposure temperature – 50-60C.
14. After the secondary curing, the finished blocks are placed on a pallet and wrapped with stretch film.
15. Ready-made products are moved to the warehouse for final curing.
Table 2: An approximate mix design for 1m3 of aerated concrete.
Dry Density, kg/m3 __________________ 700_______________600 ________________ 500
Cement, kg _________________________ 270 ________________280 __________________ 290
Sand, kg ___________________________ 390 ________________ 290 __________________ 190
Water, l ____________________________297 ________________ 256 ___________________216
CGF, g _____________________________ 544 ________________ 544 ___________________544
Na2SO4, kg _________________________ 4.6 ________________ 4.6 ____________________4.6
NaOH, kg ___________________________ 3.0 ________________ 3.0 ___________________3.0
Additional information:
The main conditions for obtaining consistently good quality:
1. Quality of raw materials.
2. Stable supply of raw materials.
3. Stability of production conditions.
The key to stable quality is also the accuracy of the dosage of all components. An increase or decrease in the quantity of any component by more than 1% leads to a change in the quality of the ready-made product.
What is the difference between Non-Autoclaved Aerated Concrete (NAAC) Blocks and Autoclaved Aerated Concrete (AAC) Blocks?
Autoclaved aerated concrete (AAC) and non-autoclaved aerated concrete (NAAC) look the same (in shape) and meet the same standard – EN 771-4:2008 (EU) and GOST 25485-89 (Russia). They have the same characteristics and service life.
A. Appearance
Autoclave blocks are always white, non-autoclave aerated concrete - from dark-grey to the light-grey.
The white colour of autoclaved aerated concrete shows the presence of lime in the composition. Grey colour of non-autoclaved aerated concrete depends on the colour of cement.
Usually, grey blocks are more welcomed in the market because they have association with concrete blocks.
B. Properties of finished blocks
The main difference is the strength of ready-made blocks.
AAC blocks are gaining final strength in the furnace. After unloading on pallets, these blocks no longer gain strength. AAC blcks are losing strength during lifecycle, especially in high-moisture conditions.
NAAC blocks continue gaining strength for another 28 days after production. The application of NAAC blocks is possible after 10 -14 days of open-air curing.
The strength of non-autoclaved aerated concrete may be increased with micro-reinforcement. Fiber yarns are added to the mixture, they provide reinforcement. The block becomes stronger and does not break after falling to the ground.
Moisture absorption. NAAC absorbs less moisture, and therefore will last longer. Comparative tests of NAAC and AAC show that the AAC unit absorps 2 times more moisture and gets wet through.
The thermal conductivity of the AAC and NAAC blocks is the same and depends on density.
Vapor permeability is also at the same level - μ=10 (10 times lower than that of air).
Hazard, health danger
The crystalline silica that is one of the main part of AAC block has been evaluated as Group 2A (carcinogenic to humans) by the International Agency for Research on Cancer (IARC).
In Australia, each pellet of blocks delivered to the construction site has to have one of the stickers with warning of its unwanted properties (Fig. 3).
Fig. 3: Warning label on AAC block palette in Australia
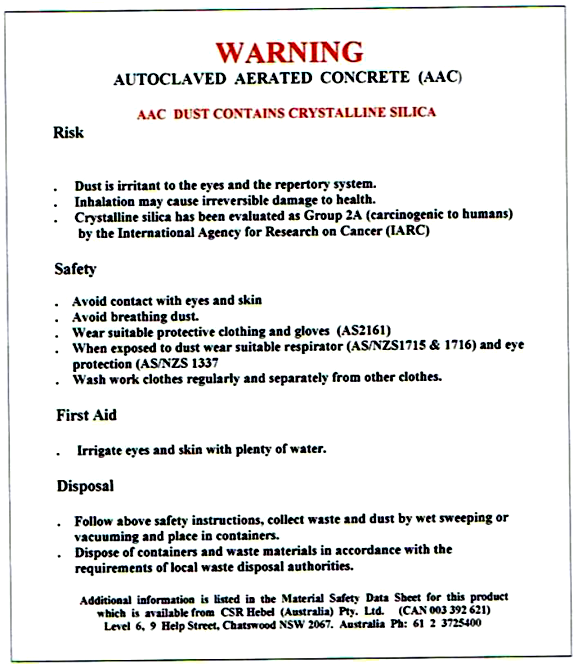
In many countries, it is prohibited to use AAC blocks for residential construction, construction of hospitals, schools and kinder gardens.
NAAC blocks are completely non-hazardous and environmental friendly construction material.
C. Composition
Autoclaved aerated concrete: silica sand, cement, quicklime, water and aluminium powder.
Non-autoclaved aerated concrete: Portland cement, filler (sand, fly ash or dolomite flour), water, aluminium powder, sodium sulphate and caustic soda.
D. Price
The production cost of NAAC block is on average 25-40%* cheaper than AAC blocks due to absence of heating processes, low energy consumption and low depreciation cost.
__________________________________
* May vary by region and country
What are available certifications and approvals for NAAC ECOCON products in the UAE and other countries?
Non-autoclaved aerated concrete refers to cellular concrete is approved for application in Russia, Ukraine, Kazakhstan and other countries.
ECOCON non-autoclaved aerated concrete blocks are certified for application in the UAE (in Emirates of Sharjah, Ras Al Khaimah, Fujairah, Ajman). ECOCON non-autoclaved aerated concrete dry mix is certified for application in Emirate of Dubai.
UAE Civil Defence authorities approved ECOCON non-autoclaved aerated concrete as fire-rated material that can be applied for fire protection of walls and partitions.
What are main construction techniques related to application of NAAC blocks?
Foundation and masonry of aerated concrete walls
Monolithic concrete beams and slab foundations are suitable for construction of houses made with aerated concrete. In this case, the walls made with aerated concrete blocks are installed on top of reinforced concrete floor cap (Fig. 4).
It is important that the foundation is levelled horizontally. The difference between the highest and lowest level should be not more than 30 mm.
Fig. 4: Installation of NAAC on top of RCC foundation

Waterproofing should be arranged between foundation and masonry. The first row of blocks is laid out on it. It is compulsory to use cement-sand mortar for fixing NAAC blocks to concrete base. Waterproofing should be done under the inside walls and partitions.
The quality of the building strongly depends on the quality of the masonry of first row of aerated concrete blocks. It is necessary to use a levelling side blocks with a rope between them in order to lay the row evenly. The correction of blocks position should be done with rubber mallet (Fig. 5).
Fig. 5: Correction of block position with rubber mallet
Fig. 5: Correction of block position with rubber mallet
Fig. 5: Correction of block position with rubber mallet

All the following rows can be laid on a cement-sand masonry mortar. As better option the special adhesive for aerated blocks (similar that is used for AAC blocks) should be applied. Usage of special adhesive allows making the dimension of 1-2 mm gap between blocks. This provides absence of heat bridges and reduction of plaster thickness.
As you can see on the Figure 6 below, the blocks are almost on each other, without gaps.
Fig. 6: Sample of masonry work

Ready-made adhesive for aerated concrete should have a consistency that allows grooves made with gear trowel not to lose their shape. But at the same time the adhesive should not be too thick. Horizontal application of adhesive with special carriage is the best option. The thickness of the lay should be 2-3 mm as it is shown on Figure 7.
Fig. 7: Adhesive application

Reinforcement of masonry is required for strengthening the walls in respect to the wind, temperature changes, foundation movement and settling of the building. If this is not done, light cracks may appear. There are two ways of doing reinforcement. The first is mandatory. The second is rarely used, as it is usually not required.
The first way is horizontal reinforcement (Fig. 8).
When the thickness of the block is 200 mm and more , it is necessary to prepare two grooves at the 60 mm distance from each edge.
Fig. 8: Horizontal reinforcement of NAAC masonry
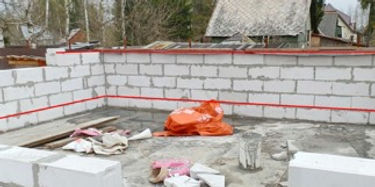
It is necessary to use 8 mm steel corrugated reinforcing bars as it is shown on Figure 9. For connection of two cores it is enough to lay them overlapping on distance not less than 300 mm.
Fig. 9: Application of steel reinforcing bars
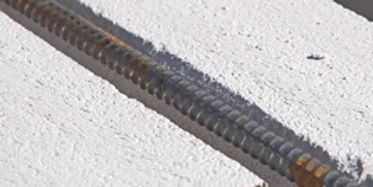
Grooves on the corners should be the necessarily rounded as it is shown on Figure 10.
Fig. 10: Corner groove

Grooves should be filled with adhesive at 2/3 depth prior to laying rebars as it is shown on Figure 11. After pressing rebars into the grooves, the excessive glue should be removed with spatula. All dust and crumbs appeared after cutting grooves should be removed with brush.
Fig. 11: Groove filling
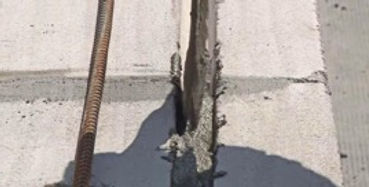
The second method is vertical reinforcement.
It is performed in the corners and some walls of the building in order to tie the foundation with the upper monolithic beam (Fig. 12). It provides additional stability of the building against the wind, but at the same time increases the heat bridges square.
Fig. 12: Vertical reinforcement of aerated blockwork

What problems could arise in relation to high-humidity and hot climate conditions?
It is well known that all cellular concrete is a capillary-porous system characterized by a high d moisture absorption (up to 35-45%) and at the same time a high ability to release moisture to the environment.
Thus, from the given data it follows that cellular concrete structures should be protecting from environmental influence in order to preserve high thermal insulation properties of the external walls. It is important to protect walls from rain, moisture, and solar radiation. Inside walls should be also protected in order to avoid direct contact of the material with water or steam.
There are several types of exterior facades: plaster, stone or brick finishing, suspended materials (siding, lining, etc.).)
1.Plaster
In countries with warm and humid climate, it is possible to finish NAAC block walls with ordinary cement-based plaster (Fig 13).
Fig. 13: Building constructed with ECOCON lightweight blocks finished plastered facade
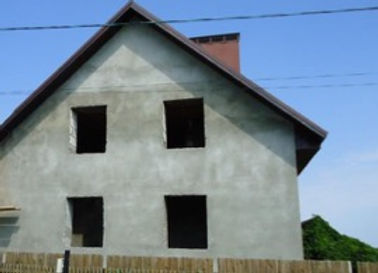
2.Siding
Finishing of the facade of the building constructed with aerated concrete blocks by using siding is essentially the same as the installation of any other cladding (Fig. 14).
The main difference is that slightly different mounting materials are used.
Fig. 14: Building constructed with ECOCON lightweight blocks finished siding

What types of production lines does ECOCON offer to customers? What are main equipment components?
ECOCON offers three types of affordable plants for producing NAAC blocks:
ECOCON-ASM-40CA
ECOCON-ASM-100CA
ECOCON-ASM-200CA
The difference is in production capacity, that is 40 m3, 100 m3, 200 m3 per day (24 hours) respectively.
The level of automation of these lines is almost the same (except for the automated cutting machine RM-4 CNC, which is included only in the configuration of the line ECOCON-ASM-200CA).
Fig. 15: Main equipment components of ECOCON-200CA plant
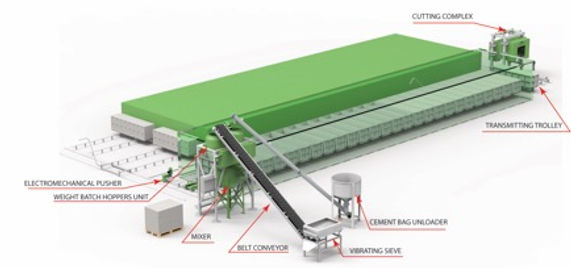
Automated cutting allows to produce u-shaped blocks, blocks with grooves, with handles, as well as automatically cut the hump. After selecting the desired program, the complex itself takes the billet with a cart, cuts it and sends the cut-into-blocks billet to the heating chamber. The whole process takes only 6 minutes.
In addition, forms that are used in ECOCON-ASM-200CА plant are 2 times larger and are designed for 24 blocks (instead of 12 blocks in ECOCON-ASM-40CA and ECOCON-ASM-100CА plants).
The mixer in ECOCON-ASM-200CA is also designed for a larger volume - 0.86 m3 (instead of 0.45 m3 in ECOCON-ASM-40CA and ECOCON-ASM-100CA plants).
Technological Process:
● Belt conveyor feeds sifted sand from vibrating sieve and/or sand hopper into the unit of weight batch hoppers.
● Screw conveyor is supplying cement from silo or big bag unloader.
● The weight batch hoppers unit weighs the components in the required proportion and feeds them into the mixer for further preparation of the mixture.
● Electro-mechanical pusher smoothly moves forms to the preheat chamber. With the help of a self-propelled transmitting trolley, the aerated concrete billet is moved to mechanized/automated cutting complex and then to a heating chamber.
● After removing the ready-made blocks, form’s platforms are ready to resume the cycle.
What are main maintenance procedures related to ECOCON plant operations?
Maintenance is recommended twice a year.
Activator-type mixer:
1. Check-up and replacement (if necessary) of mixer propeller - 4 PCs.
2. Check-up and replacement (if necessary) of bearing 180307 - 4 PCs.
3. Check-up and replacement (if necessary) of belt B(B)-1500 - 6 PCs.
Cutting complex RM-4:
Check-up and replacement (if necessary) of:
1. Cutting wire - 3 coils
2. Bearing UCP-207 - 4 PCs.
3. Bearing 2202-2RS - 3 PCs.
4. Bearing 1000900 - 6 PCs.
5. Steering rod end (short) - 2 PCs.
6. Steering rod end (long) - 2 PCs.
7. Nut M14*1,25*10 of engine suspension, pivot pin front. suspension, tip R/t (16101511) - 4 PCs.
8. Tie rod steering VAZ-2101-2107- 2 PCs.
9. Cutter for handles - 1 set.
10. Sensor F8002645 SIENA-M12B-PS-K-L-P5-
Mold sides with reinforced fasteners:
Check-up and replacement (if necessary) of:
Latch 703 L/C - 100 PCs.
Pusher 0,75 kW:
Check-up and replacement (if necessary) of:
Limit switch - 10 PCs.
Belt conveyor:
Check-up and replacement (if necessary) of:
Chevron tape with lock - 1 PC.
Vibrating sieve:
Check-up and replacement (if necessary) of:
Vibration insulator - 8 PCs.
How much time is required for setting up ECOCON plant?
The period of manufacturing and delivery is approximately:
60-70 days (2-3 months): engineering, approval of drawings, purchasing of components;
30 – 40 days (1 month): manufacturing process;
30 days (1 month): delivery
10 – 15 days (0.5 month): installation, trial run, handing over.
What are details of possible technology transfer?
Delivery is carried out by the appointed logistic company. The exact cost and delivery time can be specified on request.
ECOCON technologist will come to you for equipment commissioning and training. We will provide you with a mix design of aerated concrete in accordance with local conditions, raw materials and market requirements.
ECOCON technologist will carry out all calculations based on the characteristics of your raw materials, cement grade, sand fraction, batch of chemical components and provide a recipe that will give you the desired result.